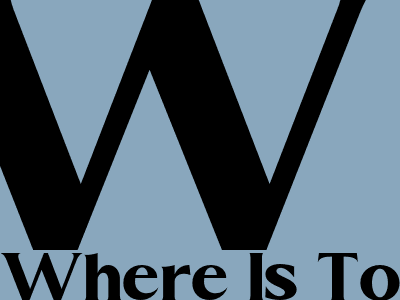
Toilet Paper Production: Unraveling the Manufacturing Process
The Global Reach of Toilet Paper Production
Toilet paper is an essential household item found in bathrooms worldwide. The manufacturing of this ubiquitous product involves a complex process that has evolved over the centuries.
Globally, toilet paper production is dominated by a few major players. The largest producer is SCA, a Swedish company that operates in Europe, Asia, and North America. Other major producers include Kimberly-Clark (United States), Procter & Gamble (United States), and Georgia-Pacific (United States).
The Raw Materials of Toilet Paper
Pulp: The Foundation of Toilet Paper
At the heart of toilet paper production lies pulp, a fibrous material derived from trees. The most common type of pulp used is virgin pulp, which is made from trees that have been specifically grown for paper production. Recycled pulp, made from used paper products, is also utilized to reduce environmental impact.
Water: An Essential Ingredient
Water plays a crucial role in the toilet paper manufacturing process. It is used to soften the pulp and create a slurry that can be easily processed. Water is also used to clean the paper during production and to form the finished product.
The Manufacturing Process: Step-by-Step
Pulping: Breaking Down the Fibers
The pulping process involves breaking down the wood fibers into a slurry. Mechanical pulping uses grinders to grind the wood into small fibers. Chemical pulping dissolves the lignin, a substance that binds the wood fibers together, using chemicals.
Papermaking: Forming the Sheet
The pulp slurry is then poured onto a wire mesh conveyor belt. Water drains through the mesh, leaving behind a thin layer of fibers that forms the base of the toilet paper sheet.
Pressing: Removing Excess Water
To remove excess water, the paper sheet is passed through a series of rollers. The pressure applied compresses the fibers and removes water, making the paper stronger.
Drying: Achieving the Desired Texture
The wet paper is then dried in a heated dryer. Different temperatures and drying times can create varying textures and thicknesses for different types of toilet paper.
Embossing: Adding Patterns and Designs
Embossing is an optional step that adds patterns or designs to the surface of the toilet paper. Heated rollers with raised patterns are used to create the desired effects.
Cutting and Packaging: Finishing Touches
The finished toilet paper is cut into rolls, wrapped in plastic, and packaged for distribution.